In Situ Chemical Oxidation (ISCO)
Learn How Oxidants Are Used To Destroy Environmental Contaminants
Hire DeepEarth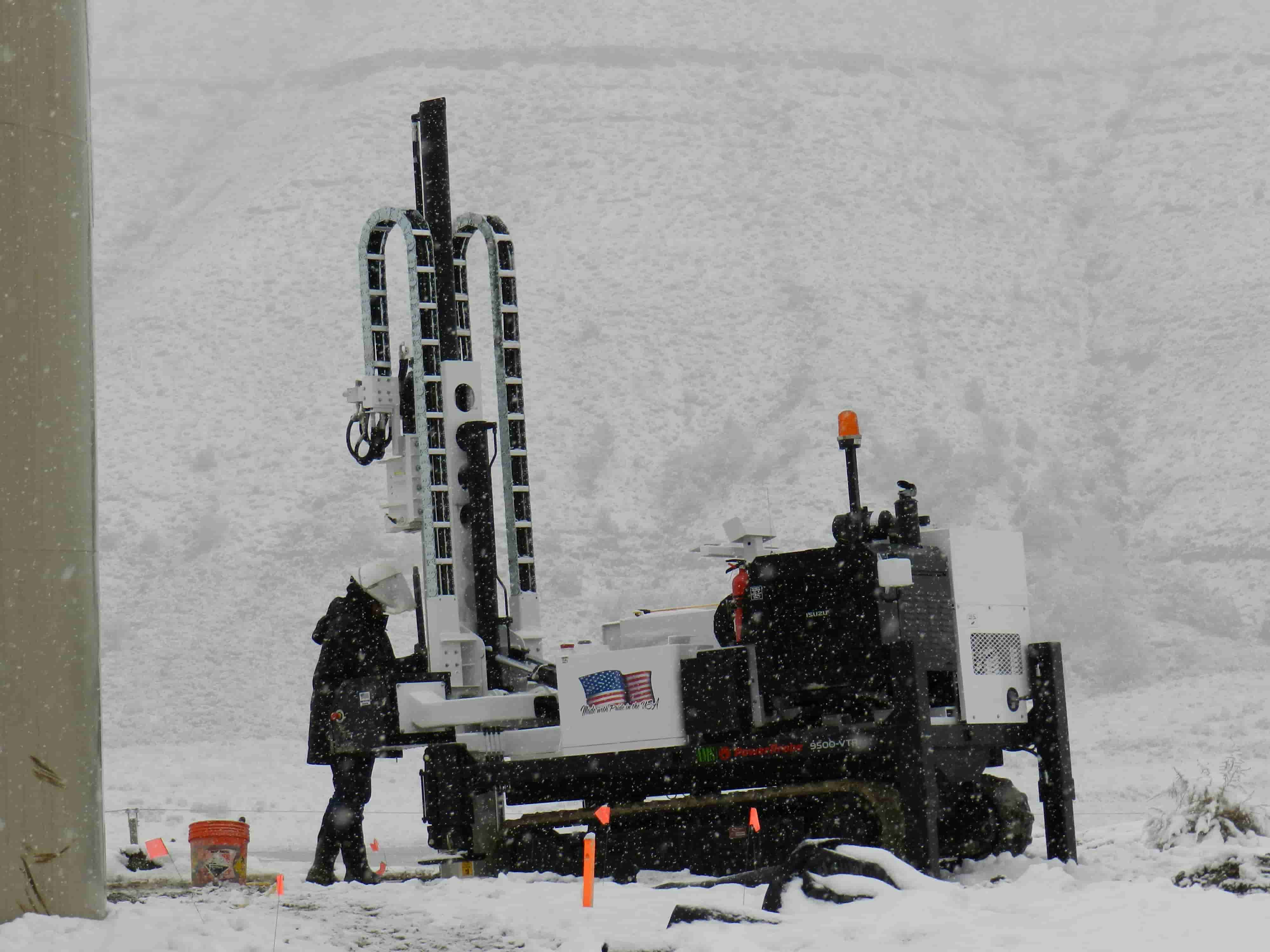
What Is In Situ Chemical Oxidation (ISCO)
In Situ Chemical Oxidation is an environmental remediation technique used to bring contaminants found in soil and groundwater down to acceptable levels. The process involves using chemical oxidants to begin an advanced oxidation process. This oxidation process is what then destroys the contaminants.
ISCO is the counterpart to In Situ Chemical Reduction. Together they form a redox reaction. ISCO being "ox," and ISCR being "re." Studies have shown chemical oxidation alone to be relatively ineffective when dealing with chlorinated solvents and even some gasoline-related compounds. However, many common contaminants do respond positively to oxidation independently.
However, when both ISCR and ISCO are combined, and the redox reaction is created, it's far more effective than either method in isolation. When combined, the resulting reaction can quickly destroy chlorinated solvents, petroleum hydrocarbons and gasoline-related compounds.
Common Chemical Oxidants
There are more oxidants used today than the ones below, but these are by far the most common. We here at DeepEarth use a modified Fenton's Reagent, so we'll start off by describing that.
Fenton's Reagent
Fenton's Reagent is typically a mixture of hydrogen peroxide and soluble iron to form hydroxyl radicals. These hydroxyl radicals are used to oxidize contaminants. Studies show that this method is very effective on contaminants like chlorinated solvents, BTEX, and even long-chain hydrocarbons.
The benefit of traditional Fenton's reagent is that it's a process that uses very inexpensive materials, and the process is very fast acting and aggressive. It's also been known to destroy contaminants in groundwater in addition to oxidizing contaminants.
However, more traditional Fenton's reagent can be very exothermic when large amounts of various things are present in the contaminant zone. Anything from iron, manganese, or NAPL contaminants can cause the oxidation process with this oxidant to produce extreme heat.
Modified Fenton's Reagent
Fenton's chemistry as it stands - when in contact with high concentrations of certain contaminants - can produce a lot of heat. This heat can then result in vapors being created from both groundwater and contaminants that then escape from the subsurface.
However, Fenton's reagent can be modified in many different ways to improve upon it to avoid these drawbacks entirely. Our Cool-Ox® technology is actually a form of modified Fenton chemistry. Using our patented process, we are able to oxidize and effectively destroy several organic contaminants such as hydrocarbons, halogens, chlorinated solvents, MGP and even brine all without creating an exothermic reaction. Meaning - no heat will be generated in the treatment zone!
In addition to our modified and patented oxidant not putting off any heat, there are also no harmful byproducts created and left behind. Meaning no corrosion either. And, unlike other oxidants, we have no need to add any more metals (iron) to the treatment zone. In fact, all soil naturally has enough iron present to act as a catalyst using our patented Cool-Ox® technology.
Studies On Our Unique Modification To Fenton Chemistry
We have carried out several studies comparing these main four oxidants to see which is the most effective. In fact, one of our studies shows The Effect of the Four (4) ISCO Oxidants on PCE Oxidation, and in the study it was proven that our patented reagent (Cool-Ox®) was the most effective.
It not only destroyed the contaminant, but it didn't leave behind any harmful byproducts. In addition, it effectively destroyed the target contaminants without causing an exothermic reaction (meaning no heat), and all while increasing the counts of native soil microorganisms.
Due to this and many other studies like this, we believe this form of a modified Fenton's Reagent to be by far the most effective method to achieve complete free product destruction.
The only issue with Fenton's reagent is the lack of stability found with hydrogen peroxide. Due to this lack of stability, we instead have modified Fenton's chemistry to work using an aqueous suspension of solid peroxygen compounds. These compounds then hydrolyze to create hydrogen peroxide.
Because hydrogen peroxide is being created as a result of the reaction, the lack of stability is no longer an issue. In addition to this, due to the relative insolubility of these compounds, it ensures that these oxidizers can be produced over a long period of time, ensuring maximum effectiveness.
Learn How Our Cool-Ox® Technology WorksPermanganate
This ISCO treatment is usually used in one of two forms - sodium permanganate or potassium permanganate. The benefit of using permanganate is that it is very slow in terms of how it reacts in the subsurface. Due to this slow reaction, it can spread further and oxidize more of the treatment zone.
However, one main drawback is the byproduct this oxidant creates. The byproduct tends to bind sand particles into a cement-like substance, making it difficult for water - and the permanganate itself - to go through to other areas in the subsurface. In other words, it ruins the effectiveness of the oxidant unless the byproduct is extracted before it can solidify.
Sodium Permanganate
Sodium Permanganate is more expensive than potassium permanganate, but it's also much more soluble and, as a result, can be administered in much higher concentrations.
Potassium Permanganate
Potassium Permanganate, while less expensive, is much less soluble. It must be soaked in water and dissolved before it can be administered. Due to the need to be dissolved before treatment, it is typically used in a lower concentration than sodium permanganate. In addition to needing to be administered in lower concentrations, potassium permanganate's solubility is largely dependent on temperature
In fact, permanganate will often solidify once applied to the contamination zone. While solidified, it will be unable to oxidize the contamination. In time, it will become soluble once again and liquify, but this is a very prolonged process.
Persulfate
Persulfate is one of the newest forms of ISCO treatment around today. Because it's so new as an oxidant, and there have yet to be many studies done on its effectiveness in the field, it still isn't as widely used as other oxidation methods. One of the most significant issues with it as an oxidant is that when persulfate is mixed with the catalyst (ferrous iron), it creates an incredibly corrosive reaction that has been shown to eat through various metals and materials also present in the treatment zone.
Ozone
While this is a very strong oxidant, the main issue is that it is very difficult to control. This oxidant is a gas, and as such, it doesn't act like the others on our list. First off, it requires a distribution from below the bottom up. Meaning you need to administer it from below the bottom of the contaminant.
In addition, when the gas is released, it tends to go the path of least resistance and exit the subsurface immediately. In contrast, other methods will remain where injected and will mix and spread throughout the material.
Ozone also tends to react with the things naturally found in soil and groundwater - minerals, organic matter, etc. Whereas the other oxidants react mainly or entirely with the contaminant and nothing else.
What Contaminants Does ISCO Treat
As an advanced oxidation process, ISCO is commonly used to treat compounds related to gasoline and chlorinated solvents. However, chemical oxidation is rarely done on its own. It's usually done with in situ chemical reduction to create a redox reaction, thereby maximizing the remedial benefits.
When these two methods are combined, we can destroy several contaminants such as hydrocarbons, halogens, MGP, and brine.
How Long Does Chemical Oxidation Take
It can take anywhere from weeks or even years to treat a site. The length of time depends on various factors such as the size and type of site, the type and concentration of contaminants present, and even the budget can change the time required to treat a site.
In ideal situations, it's more than possible to treat a site once and have the treatment be a success in as little as a few months. Not all remedial projects are ideal, however, and to best determine how long it might take to treat your site, you can always get in touch with us and ask one of our environmental specialists.
When Should You Use ISCO?
If your site is contaminated with hydrocarbons, halogens, brine, or MGP, it's safe to assume in situ chemical oxidation would be a good investment. Not only is it incredibly safe, fast-acting, and environmentally sustainable, but there is also no need to spend money on excavation. "In situ" is Latin for "in place," meaning it happens on-site.
Not to mention the most common method to administer the oxidants into the subsurface is via DPT, meaning there are also no contaminated drill cuttings to dispose of either. Meaning ISCO is not only an incredibly effective remedial solution, but it's also one of the most cost-effective methods used today.
Ultimately, it depends on what your environmental consultant finds during their site assessment.
What Methods Are Used To Implement In Situ Chemical Oxidation
The methods listed below are by no means all of the methods used today in ISCO, but they are some of the most commonly used in situ remediation technologies available today.
Direct Push Technology
Direct push drilling is one of the most common and reliable remediation technology to date. DPT is a method of using a direct push rig together with a hydraulic hammer that then drives hollow probes to the desired depth. Unlike traditional rotary drilling, this method leaves no contaminated drill cuttings behind.
DPT is the process we specialize the most in, as our teams have been successfully closing sites for more than two decades. We have a specialized process for how we carry out this process, and if you want to learn more about our method, you can learn more on our DPT page.
Soil Mixing
Soil mixing is a method where an excavator or other digging equipment mixes the oxidant with the soil. Soil blending is typically our first choice because we ensure that the entire contaminant mass comes into contact with the reagent for the best chance to destroy organic contaminants present in soil and groundwater.
Typically soil blending is best when used on smaller contaminant areas. Still, it is the most effective when it can be used because our specialists can ensure the best and most thorough application possible. Especially if the treatment zone is comprised primarily of contaminated soil.
Hydro-Dart™
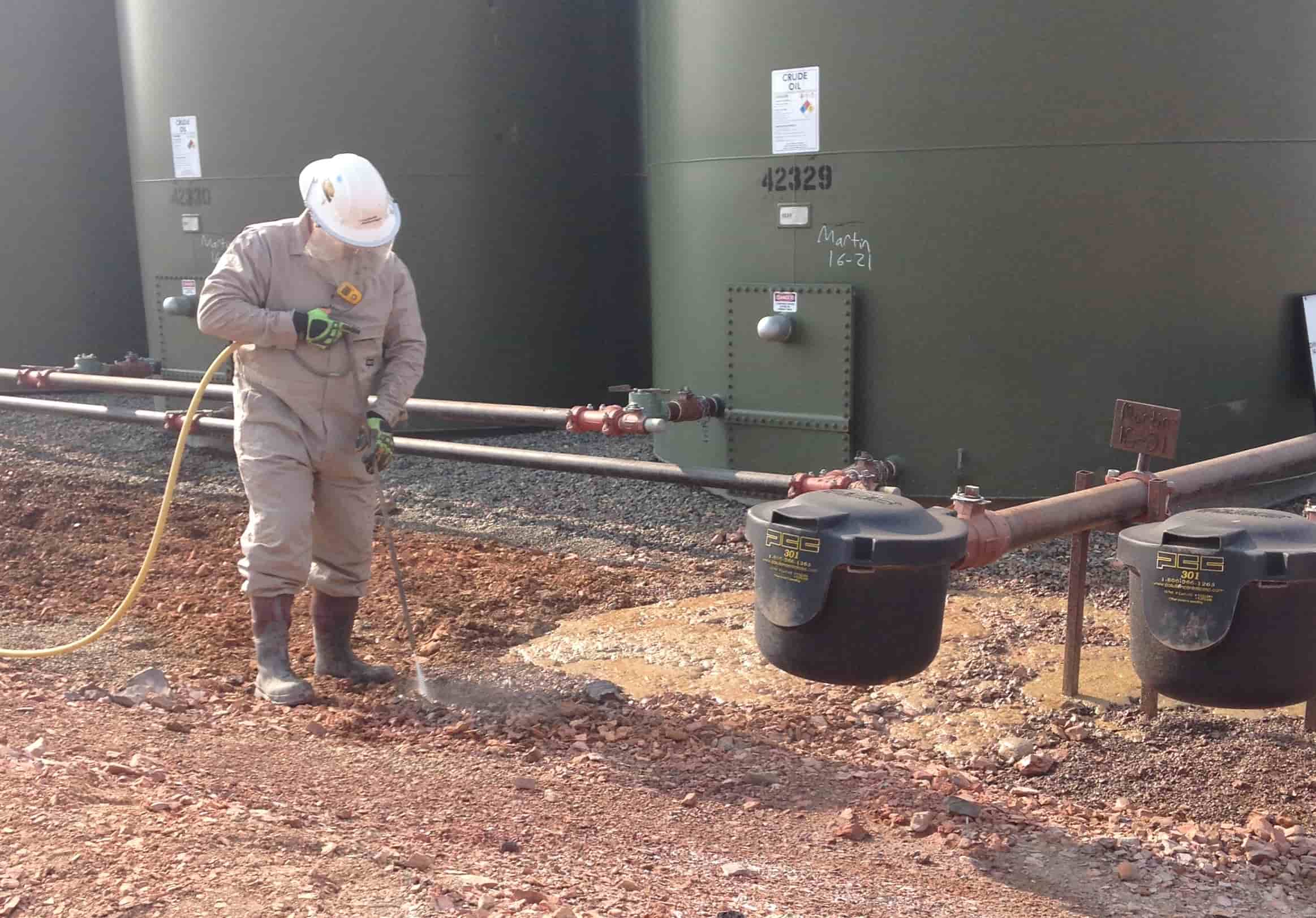
While this technology is unique to DeepEarth Technologies, Inc., it has proven to be incredibly effective for contaminated soil and groundwater remediation at or less than 12 feet below the subsurface. Using pressurized water jets we are able to mix water and our patented reagent in our hand lances to completely cut through and saturate the contaminant zone.
Our Hydro-Dart is one of the least invasive options available. We can analyze the reaction on the surface of the treatment zone, as this remediation technology results in a thick foamy reaction that happens once the reagent has started to destroy organic contaminants.
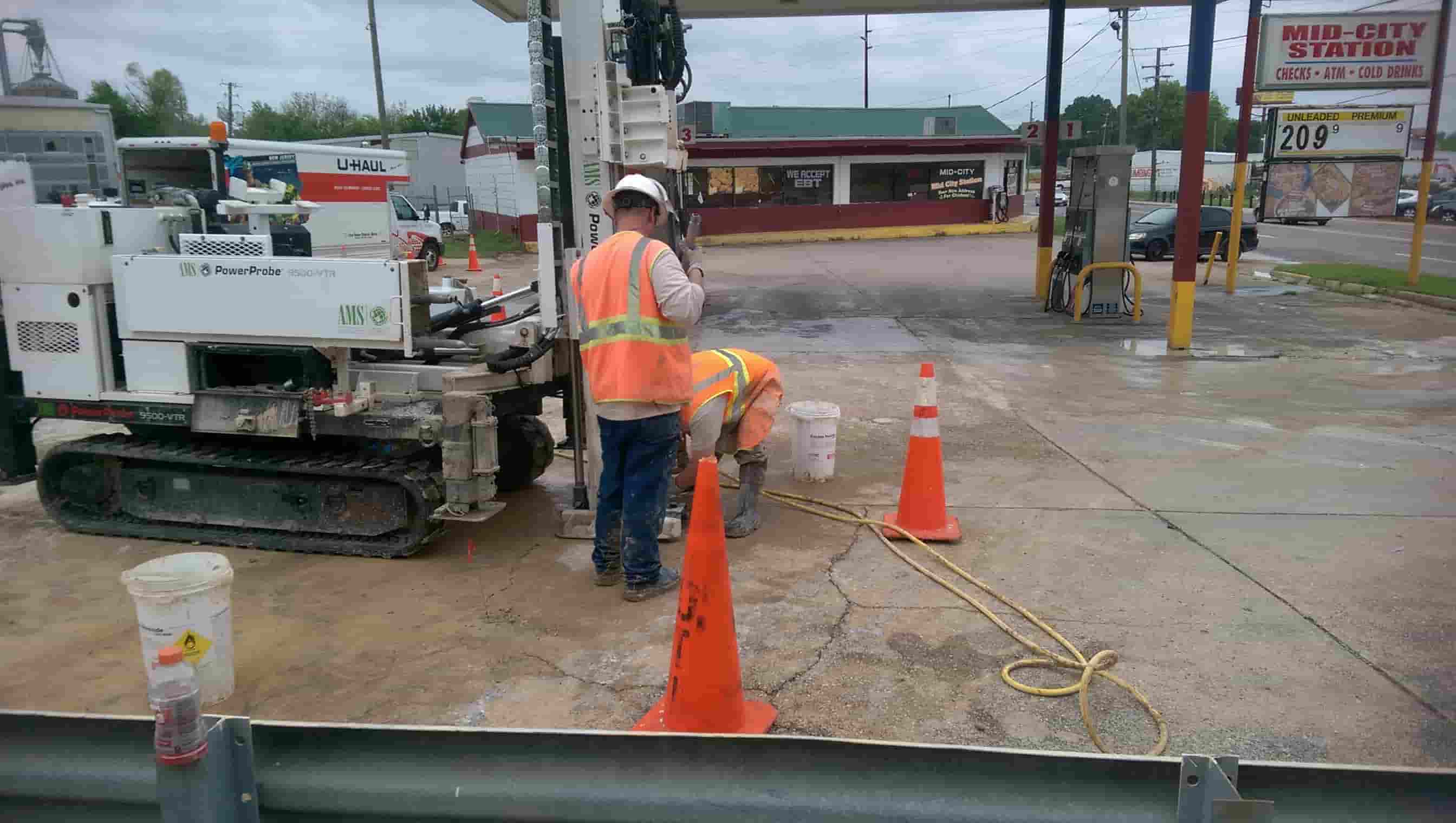
Why You Should Choose Us For Your In Situ Needs
For more than two decades, our team has won several awards for our environmental remediation services. Our patented technology continues to be the only technology that will destroy organic contaminants without:
- corrosion
- creating heat
- Pore Clogging
- Toxic by-products formed with anaerobic dechlorination
- DCE - DCA - VC - Methane
- Long Drawn-Out Bioremediation Products
- SAR Exacerbation
- No Sodium or Potassium
When you choose DTI, you're choosing true environmental sustainability. Not only will you get your site back, but our technology will help to bring the balance back to the delicate ecosystem underneath your feet. Not only does our technology destroy contaminants without any of the drawbacks listed above, but also, once the oxidation process has been completed - what is left behind has been proven to increase the count of native soil microorganisms that encourage plant growth.
Get Your Site Back Today
If you've got a site contaminated with hydrocarbons or chlorinated solvents, MGP or brine, you can either give us a call, request a quote, or contact us with any questions to be connected to an environmental specialist.
Request A QuoteGive Us A Call