Monitoring & Recovery Well Injections
Remedial Solutions For Even The Most Difficult Sites.
Hire DeepEarth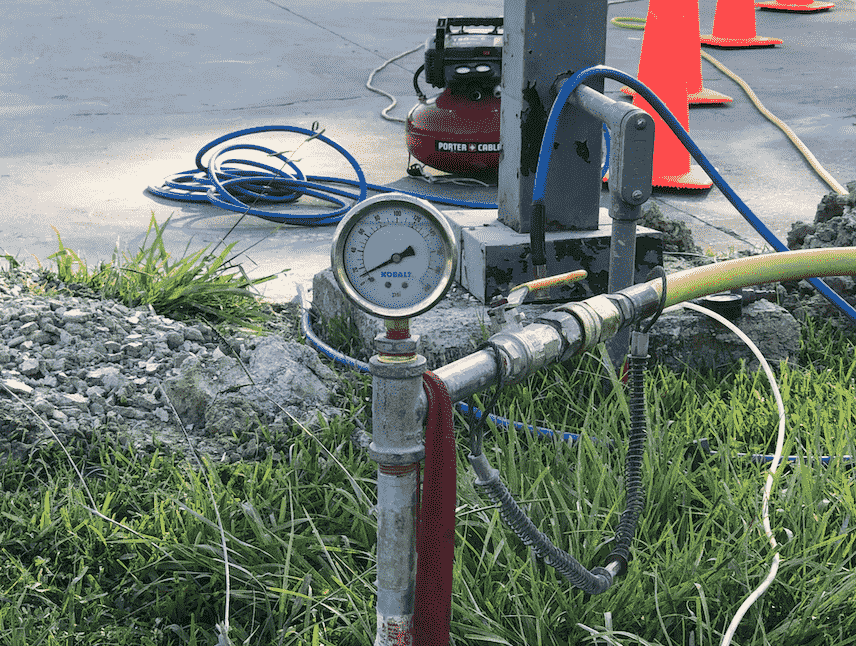
Applications
Our Monitoring & Recovery Well Remediation Process
DeepEarth Technologies, Inc. (DTI) utilizes many different application methods. One of these application methods is the use of packers to inject Cool-Ox® into onsite wells. DTI can inject into 2” and 4” wells utilizing Packers (see images below).
DTI places the packer at the top of the well casing and inflates it using an air compressor until a snug fit is achieved. Once this is achieved, the shut off valve is closed, and the air line to the compressor is disconnected.
Once the packer is in place, DTI connects the injection hose and begins the injection process. The use of packers for this type of application ensures that the Cool-Ox® reagent is injected under pressure (± 100 PSI) in order to push the reagent out of the screened interval and into the groundwater zone. Both the air line and injection line are fitted with appropriate pressure gages and shut off valves in order to minimize chance of failure.
Although this is not the preferred application method, well injections have been used by DTI many times when other methods alone are either not an option or not enough to reach our client’s goals.
During the application design phase of any project where well injections become feasible, well (MW, RW, IW) construction logs and any other installation data/diagrams will be requested by DTI to determine integrity and injectability of the onsite well/s.
When Should You Choose Well Injections
In most cases, using other methods to treat your site will make more sense. However, in some rare situations, other solutions are not viable. Below we'll discuss some common reasons well injections might make the most sense to clean up your site.
Soil Type
Our primary services are our DP injections, as well as soil mixing services. We bore down below the subsurface using our DP rig and administer our patented reagent. We have successfully treated several sites with limestone and/or cobbles. However, in some rare cases, the soil type consists of too much limestone and/or cobbles, and our drilling equipment cannot safely make it to the required depth. In these situations, using the existing recovery wells to treat contaminants makes more sense.
Budget
Well injections are the most affordable remedial service we offer at DTI. If you have an existing extraction or monitoring well but don't have a large budget to clean up your site, this would be an excellent fit for your project.
Small Footprint
Most businesses require as little - and if possible no - impact on day-to-day operations. Meaning the smaller the footprint, the better. Due to the minimal footprint of our other remedial solutions, it often makes more sense to use more robust methods to close your site. However, in extreme situations requiring us to minimize the impact on their operations as much as possible, it may make sense to use our monitoring & extraction well injections.
Applications
Which Types Of Contaminants Can Be Treated?
We can treat all sorts of contaminants by injecting monitoring and recovery wells with our patented technology. Our technology has been proven to destroy several contaminants.
Using this treatment method combined with the power of our remediation products, we can destroy hydrocarbons, halogenated compounds, MGP, and brine. In fact, we also share how we were able to successfuly treat a site contaminated with paraffin down below.
Basically any contaminants that can be destroyed by chemical oxidation or reduction can be destroyed with our well injection services.
Paraffin Clearing
Paraffin clogged recovery well at an oil producing wellsite in extreme northern Utah. Three DPT injection points had been injected with Cool-Ox® a distance of approximately 5 feet from the well. Small bubbles of CO2 can be seen in the paraffin/NG condensate in the recovery well.

As the Cool-Ox® reaction proceeds, larger diameter bubbles can be seen at the surface of the well. Also, it can be noted that the hydrocarbon liquid level in the well has risen to the point where it is nearly ready to run over. This is due to the ongoing generation of CO2 as the oxidation reaction proceeds.
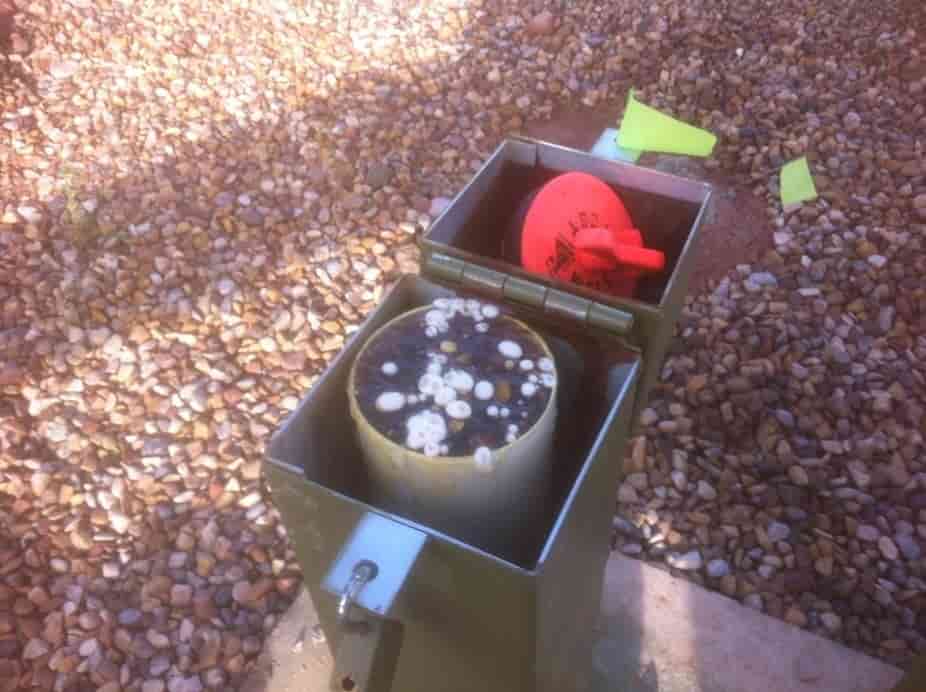
As Cool-Ox® continues reacting with the hydrocarbon waxy long-chain alcohols are produced that, when expelled from the well, give the appearance of a heavy, cheesy foam. At this point, much of the paraffin has been converted to alcohols. These alcohols, having surfactant properties, can now align with water in the same fashion as manufactured detergents (wetting agents) and the water and gas (CO2) is now the transport mechanism for clearing the well.
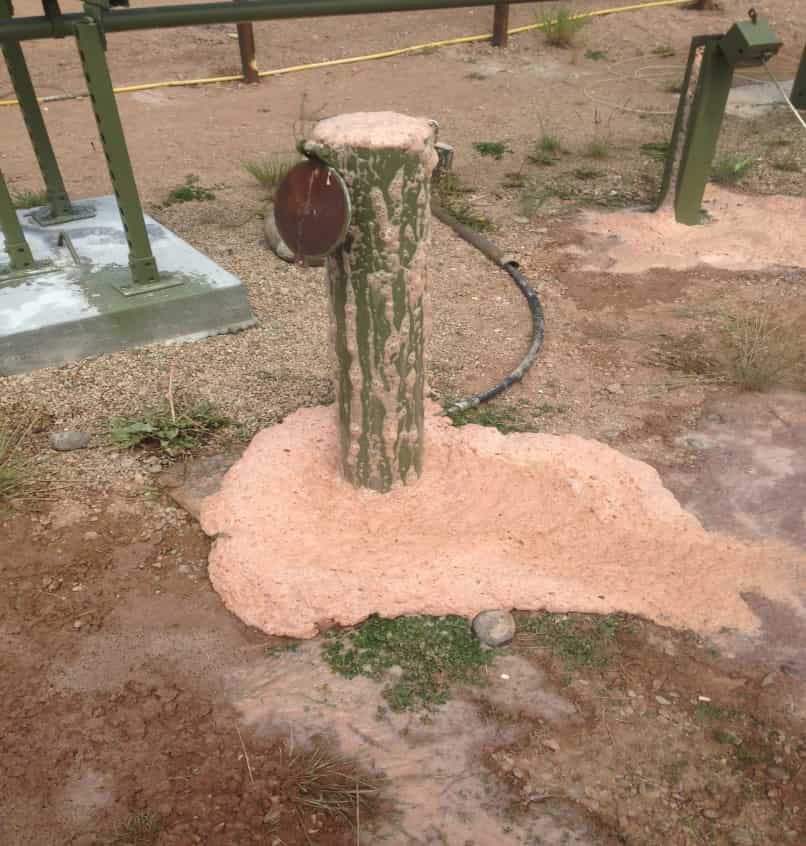
This well, located approximately 30 feet from the previous injection point array, is also demonstrating the reactions that cleared the previous well. Paraffin impacted condensate can be seen as the amber liquid present in the foam.
Approximately five minutes after the photo is taken, all of the paraffin impacted condensate had been reacted and was then present as foam. This is the same reaction that proceeds when Cool-Ox® is injected as a remedial process to decontaminate service stations, pipelines, refineries and any location were hydrocarbons have been released to the environment.
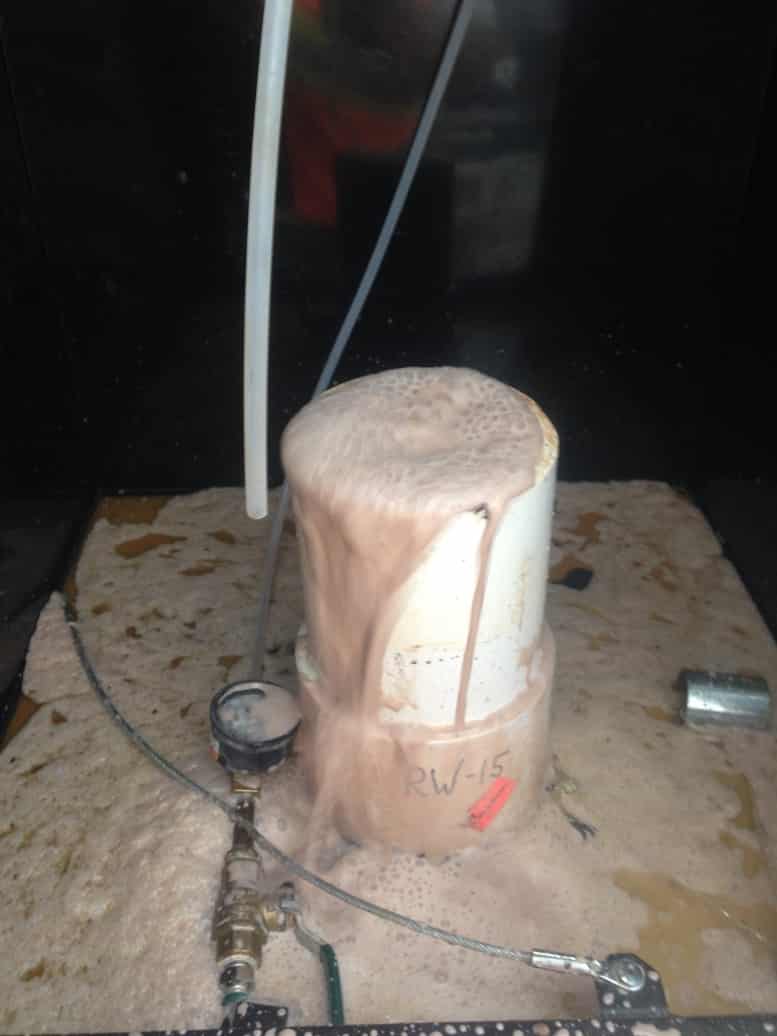